Introduction
Accurate cost estimation is essential to any building project’s success in the US. Whether it’s a big infrastructure project, a commercial renovation, or a residential construction, being able to estimate reasonable costs up front can help avoid budget overruns, missed deadlines, and financial losses. Everything you need to know about accurately estimating construction costs is covered in this guide.
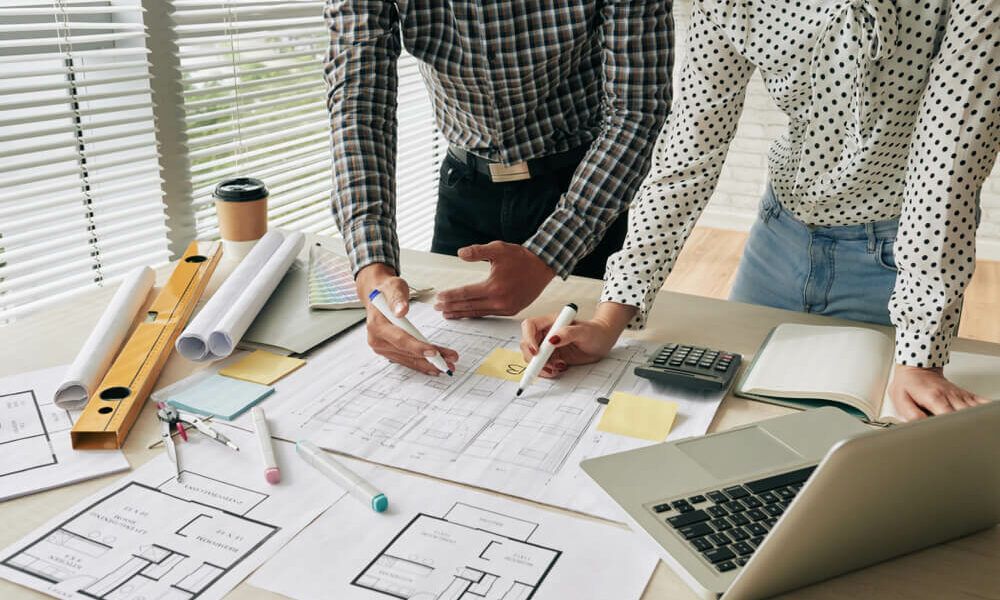
Understanding The Scope Of The Project
Determining the scope is the first step in estimating construction costs before any calculations are made. This comprises:
- Project type (residential, commercial, industrial)
- Size and complexity
- Location and access
- Design features and materials
- Permits and regulations
Accurate takeoffs and improved cost forecasting are made possible by a clear scope. It lessens the possibility of overlooked details and unanticipated costs.
Detailed Quantity Takeoff (QTO)
All cost estimates are based on the quantity takeoff (QTO). It entails quantifying each system, labour unit, and material used in the project. Estimators use engineering and architectural drawings to extract quantities like
- Cubic yards of concrete
- Square footage of flooring
- Linear feet of piping
- Units of fixtures and fittings
We can expedite this procedure and lower human error by using digital takeoff software such as PlanSwift, Bluebeam, or STACK.
Material Cost Estimation
Once quantities are defined, the next step is assigning unit costs. Material prices can vary by:
- Region
- Vendor and availability
- Quality/grade of materials
- Market volatility (e.g., steel, lumber)
We advise getting quotes from several suppliers or consulting regional cost databases such as RSMeans or Craftsman Book in order to obtain precise pricing.
Additionally, always factor in freight expenses and waste (usually 5–10%).
Labor Cost Estimation
Labor is one of the most significant and variable costs in any construction project. Estimating labor requires considering:
- Crew productivity (based on experience, project type, and site conditions)
- Union vs. non-union labor rates
- Wages, overtime, and benefits
- Local labor laws and taxes
Assign man-hours per task and divide labour into categories such as electrical, roofing, and framing. To figure out the cost per task, multiply by the hourly wage.
Example:
If framing requires 2 carpenters for 40 hours at $35/hour:
2 x 40 x $35 = $2,800 labor cost for framing.
Equipment and Tool Costs
Don’t forget equipment rental or purchase costs, especially for heavy machinery:
- Excavators
- Cranes
- Backhoes
- Concrete mixers
- Scaffolding
Include:
- Rental duration
- Fuel consumption
- Operator wages (if separate)
- Maintenance costs
Even smaller tools and consumables (e.g., nails, tape, safety gear) should be itemized for accuracy.
Subcontractor and Specialty Trades
Get quotes from several subcontractors if the project’s HVAC, electrical, fireproofing, and millwork components are outsourced. Make sure the exclusions are well documented and that their scope aligns with your project requirements.
Include:
- Supervision and management costs
- Insurance and bonding
- Mobilization fees
Before including a subcontractor, review their prior performance, timelines, and level of bid detail.
General Conditions and Overhead
General conditions are essential costs related to managing the project, including:
- Site security
- Temporary utilities
- Porta-potties
- Project management and administrative staff
- Safety compliance
Meanwhile, overhead costs include:
- Office expenses
- Software licenses
- Marketing
- Legal and accounting services
Overhead is usually calculated as a percentage of the total direct cost, often between 10–15%.
Contingency and Risk Allocation
Even the best estimates must prepare for the unexpected. Contingencies are included to cover:
- Design changes
- Weather delays
- Supply chain disruptions
- Permit delays
Although 5–10% of the total project cost is the industry standard, high-risk projects might require more. Even in the event of problems, this keeps the project on course.
Markup and Profit
To guarantee profit, a markup is applied after the direct and indirect costs have been determined. This percentage is determined by:
- Company goals
- Market competition
- Project size and risk
Typical markup ranges from 10–25%, with higher margins in complex or high-risk projects.
Example:
If total project cost = $500,000
Markup = 15%
Final estimate = $500,000 + (15% of $500,000) = $575,000
Using Construction Estimating Software
Modern tools streamline the estimating process and boost accuracy. Top software includes:
- Buildertrend – cloud-based project management and estimating
- ProEst – cost estimation with templates and reporting
- Sage Estimating – integrates with accounting tools
- CostCertified – client-interactive cost estimation
- STACK – fast digital takeoffs and collaborative features
These platforms automate calculations, reduce manual entry, and allow real-time pricing updates from vendor databases.
Creating a Final Construction Cost Estimate
Compile all the data into a comprehensive cost estimate report. It should include:
- Project scope summary
- Line-item breakdowns
- Assumptions and exclusions
- Contingency and escalation
- Terms and conditions
- Pricing validity period
This document becomes a reference for budgeting, financing, and contractor negotiations.
Common Mistakes to Avoid
- Underestimating labor productivity
- Ignoring soft costs like legal fees and inspections
- Overlooking change orders and their cumulative costs
- Failing to update material pricing regularly
- Using outdated project data or regional factors
When to Hire a Professional Estimator
Large-scale or high-stakes projects benefit from the expertise of a professional construction estimator. They bring:
- Specialized tools
- Regional cost knowledge
- Risk analysis
- Accurate timelines
Hiring a professional ensures estimates are defensible, investor-ready, and aligned with industry benchmarks.
Conclusion
It takes technical expertise, in-depth market knowledge, and a methodical approach to become proficient at estimating construction costs. You can lower risk and produce successful, profitable builds by taking a methodical approach to the process, from scope definition and takeoffs to labour analysis and contingencies.
At All Bids Estimates, we provide accurate, trade-specific construction cost estimates that help you plan smarter, bid competitively, and avoid costly surprises. Trust our expert team to turn complex plans into clear, reliable numbers—fast.